MERIT
ミネベアミツミの金型センシング統合システム
導入のメリット
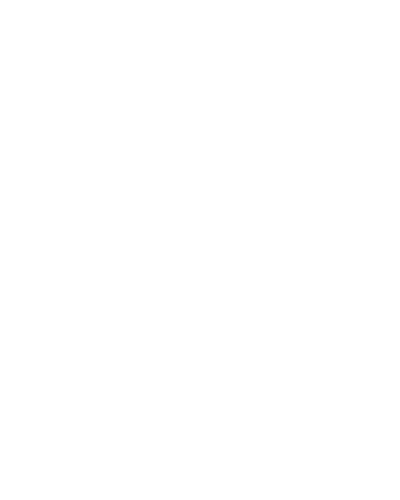
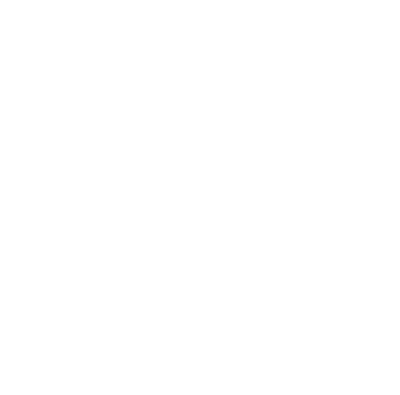
MERIT
O1
キャビティ間の成形品質均一化
- 課題
金型を図面通りに製作しても、
さまざまな要因でキャビティ間に差異が生じ、
成形品の品質にばらつきが出る
- 導入の効果
内圧波形を合わせることで、
各キャビティの重量・寸法が近づき、
均一で安定した製品品質を実現
Cav1とCav2の
波形が近づくように
金型を調整
最小限の差分に
なったことで
品質も均一に!
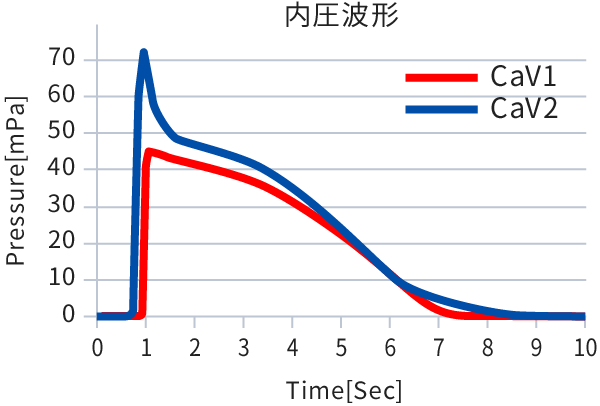
Cav1 | Cav2 | 差分 | |
---|---|---|---|
重量 [g] |
24.990 | 25.021 | 0.031 |
寸法 [㎜] |
22.745 | 22.956 | 0.211 |
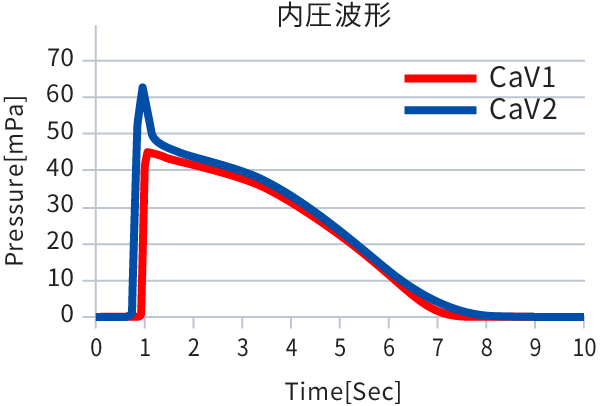
Cav1 | Cav2 | 差分 | |
---|---|---|---|
重量 [g] |
25.024 | 25.029 | 0.005 |
寸法 [㎜] |
22.916 | 22.961 | 0.045 |
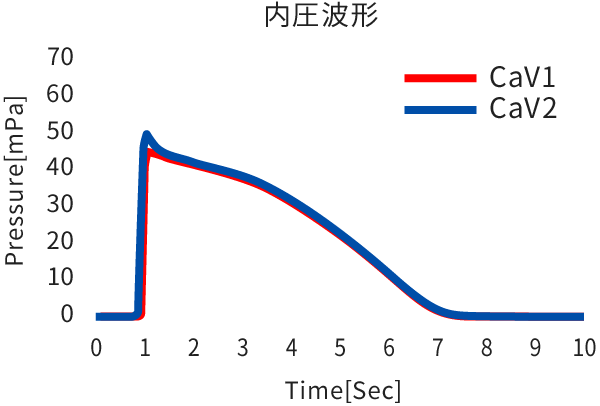
Cav1 | Cav2 | 差分 | |
---|---|---|---|
重量 [g] |
25.028 | 25.026 | -0.002 |
寸法 [㎜] |
22.949 | 22.959 | 0.010 |
波形を合わせることで、重量・寸法差分もなくなる
最小限の差分に
なったことで
品質も均一に!
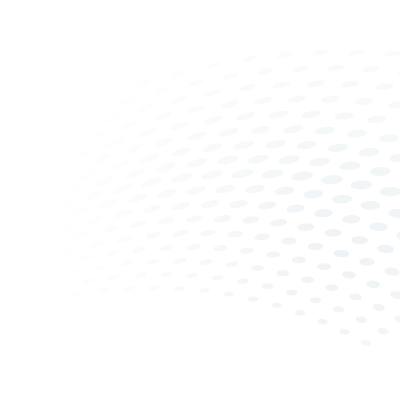
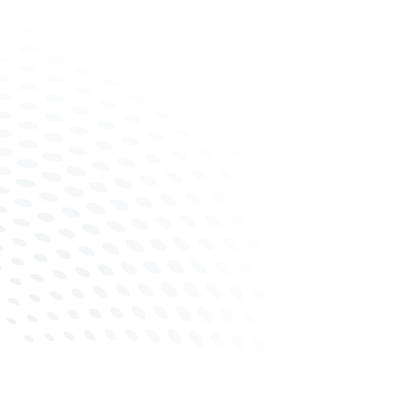
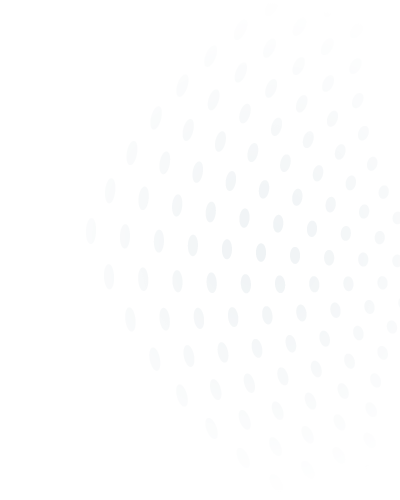
MERIT
O2
成形条件の再現
- 課題
条件出しが完了した金型を量産工場へ移管したが、
良品の成形品が出来ない
- 導入の効果
試作工場で取得した基準内圧波形に合わせて
成形条件を調整すれば、
量産工場での条件設定がスムーズになる
-
国内の試作工場で
条件出しを実施 -
条件出しで得た
金型内圧波形データを
csvファイルなどで引き渡し -
海外の量産工場では、内圧波形データに合わせて成形条件を調整することで、良品の再現がスムーズに
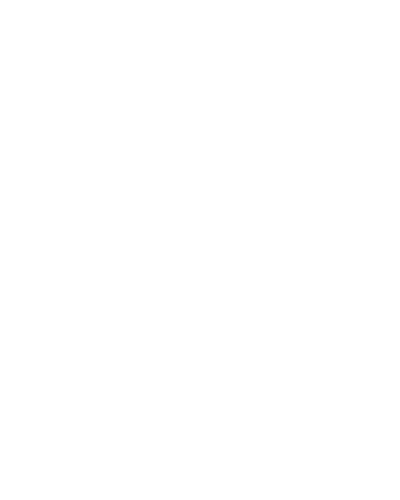
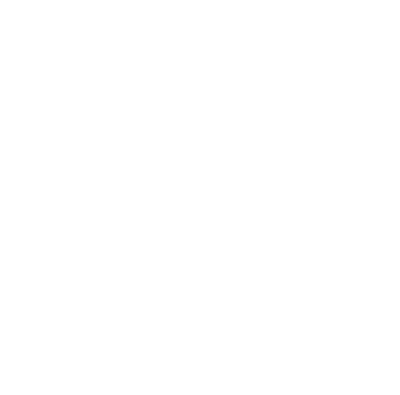
MERIT
O3
生産効率向上
- 課題
成形品の保圧時間、捨てショット数を
経験と勘により判断・設定していた
- 導入の効果
内圧や温度波形により
適切なタイミングを把握し設定することで
生産効率が向上
-
ゲートシール時間の判断
- 保圧時間を変更した際の内圧波形
保圧時間を4.0[S]から0.5[S]刻みで変更すると、1.5[S]の内圧波形で圧力が急激に下がっているため、2.0[S]がゲートシール時間と判断、データに基づいて、保圧時間の設定を必要最小限に抑えることができる
-
捨てショット数の把握
- 成形開始からの金型温度波形
成形開始から約20~30ショットで金型の温度が安定しているため、捨てショット数をデータにより判断できる
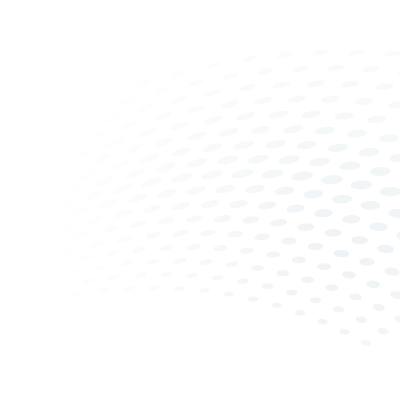
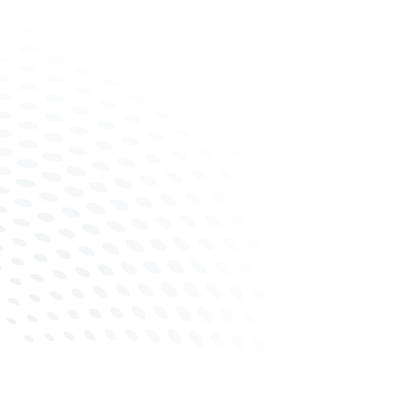
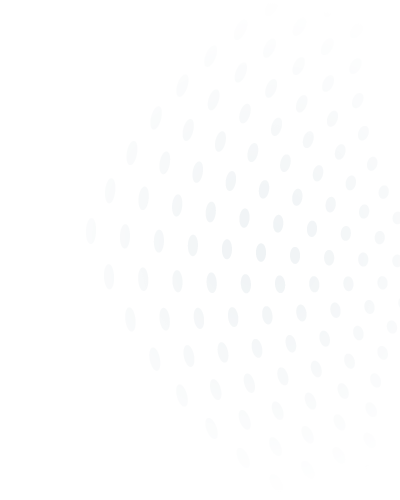
MERIT
O4
トレーサビリティ・ログ取得
- 課題
ショット毎の定量的な品質記録が残らない
- 導入の効果
内圧・温度データを出力することで
全量産品の内圧波形を定量的な品質記録として
保管、管理出来ます
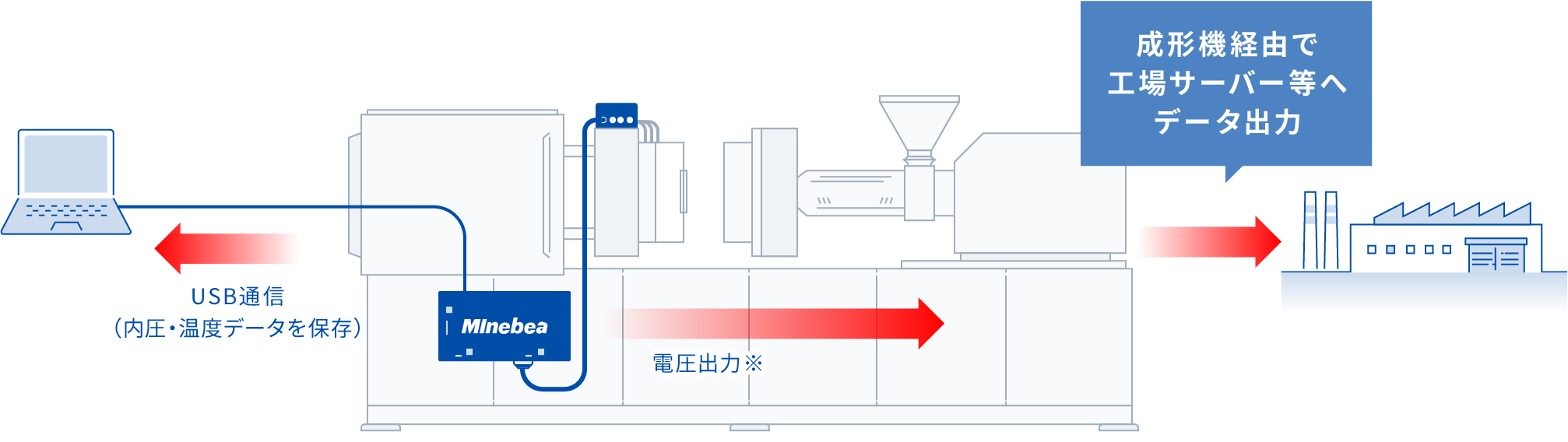
※成形機への電圧出力の接続に関しては、射出成形機メーカーとの仕様確認が必要です。
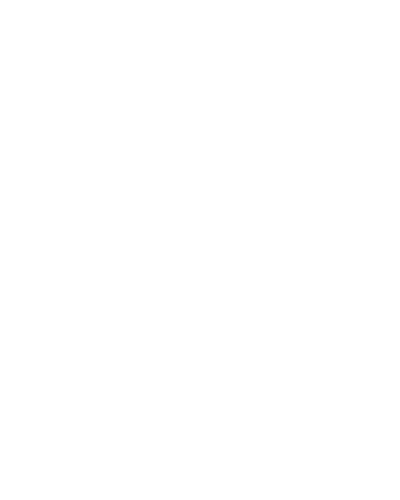
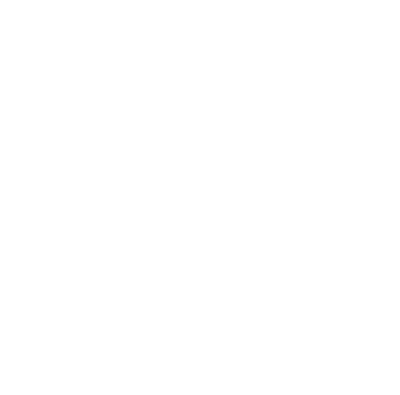
MERIT
O5
検査コストの削減
- 課題
ショートモールドが突発的に発生していたため、
全数目視検査をしていた
- 導入の効果
内圧波形でショートモールドを検知することができ、
選別が可能になったため全検査から抜き取り検査に変更、
検査にかかっていたコストを削減
A社様の場合
-
導入前
- 全検査
-
人員数168人
-
導入後
- 抜き取り検査
-
人員数81人に削減
年間にして
約850万
のコスト削減