ベアリングとエネルギー損失
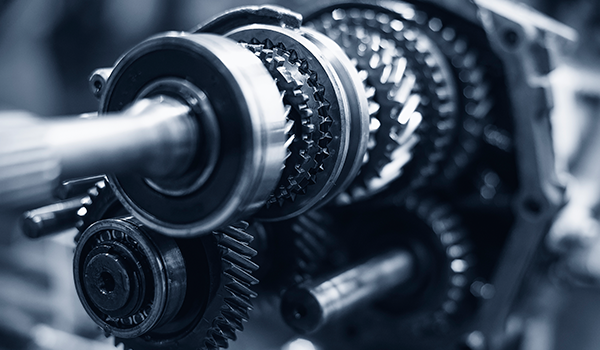
転がり軸受は転動体、内輪、外輪、保持器で構成されており、それらが接触しているため、回転時には必ず摩擦が生じます。エネルギー消費効率を高めるためには、こうした摩擦を可能な限り低減させ、エネルギー損失を最小限の抑えることが重要です。
ここでは、転がり軸受を中心にベアリングにおけるエネルギー損失について解説し、エネルギー効率を高める工夫について紹介します。
ベアリングとエネルギー損失
ベアリングはそもそも「軸を正確かつ滑らかに回転させ、摩擦によるエネルギー損失や発熱を低減させる部品」であるため、機械にベアリングを組付けている点で、すでにエネルギーロスの軽減に寄与できているといえます。しかし、回転時にベアリング自体に摩擦が生じてしまうため、摩擦によるエネルギー損失をゼロにすることはできません。
たとえばモーターが回転する場合、電源入力から実際にモーターが回りだすまでに、さまざまなエネルギー損失が発生しています。その中でもベアリングの回転による摩擦で生じる損失は「機械損」と呼ばれ、ベアリングが組み込まれたモーターや機器の出力の減衰の一因となっています。
ベアリングにおいては機械損をどれだけ減らせるかが、エネルギー効率向上のカギとなっており、そのための工夫が求められています。
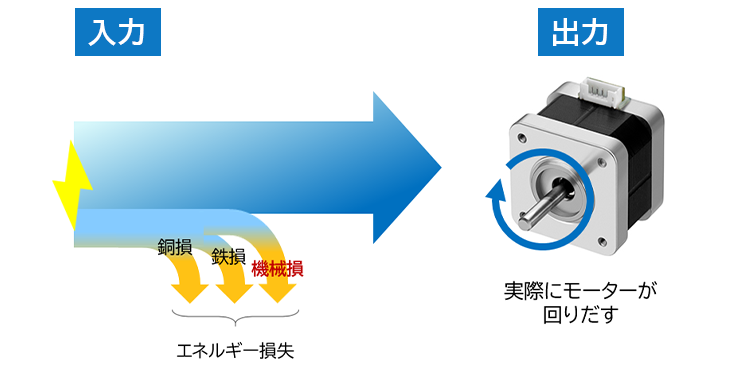
エネルギー損失が起きる原因
ベアリングのエネルギー損失は回転時の摩擦に起因しています。すべり軸受では、回転を伴わないすべり運動により「すべり摩擦」が生じます。転がり軸受では、転動体が転がることによって「転がり摩擦」が生じ、加えて、すべり軸受ほどではないものの「すべり摩擦」も発生します。
はめあい面でこうした摩擦が生じるのはもちろん、ベアリングは複数の部品で構成されているため、各部品の接触面などにも摩擦が生じます。主なベアリング内で起こる摩擦は「転動体と内輪・外輪の間に生じる摩擦」「転動体と保持器の間に生じる摩擦」「潤滑剤の撹拌抵抗」「シール・シールドと内輪・外輪の間に生じる摩擦」などがあり、こうした複数の摩擦が重なることでエネルギー損失を発生させています。そのため、エネルギー損失を軽減するためには、部品ごとの精度向上や材質の適切な選定により、各接触面において生じうる摩擦を最小限に抑えていくことが重要です。
なお、流体軸受や磁気軸受などは、流体膜や磁気浮上により非接触で軸を支えるため、設計上、摩擦は生じませんが、「流体軸受は決まった回転数でしか使用できない」「磁気軸受は絶えず電流を流し続ける必要がある」と厳しい使用条件があります。そのため、転がり軸受・すべり軸受ほどの汎用性がなく、高コストというデメリットもあります。
ベアリングのエネルギー効率を高める対策
摩擦による機械損をできるだけ軽減させるためには、ベアリングを構成する部品同士の摩擦を減らし、回転効率を高めることが重要です。そのためには、高精度なベアリングの加工・組立、予圧量の設定、機械(ハウジングやシャフトなど)への組付けなど、それぞれの段階において精度を高めていかなければなりません。
ここではエネルギー効率を高めるため、ベアリングに具体的にどのような工夫が施されているのかについて詳しく紹介します。
グリースの工夫
グリースには流動特性があり、その特性により、かかる抵抗が変わってきます。ベアリングの回転時に軌道溝内のグリースが掻き分けられる際、掻き分けられたまま留まりやすい(転動体にグリースがほとんど付着しない)タイプを「チャンネリングタイプ」、転動体表面や軌道溝内に再び絡みやすい(転動体が通った後にグリースが付着する)タイプを「チャーニングタイプ」と呼びます。モーターのように一方向に回転し続けるような用途には「チャンネリングタイプ」のグリースを使用することで、転動体が転がる際の粘性抵抗を軽減することができます。粘性抵抗の軽減により、トルクの変化を抑えることができるため、結果として連続回転する際の転がり摩擦の低減を実現できます。
一方、ごく低速で回転する際や往復回転させる用途では「チャーニングタイプ」のグリースが適しています。抵抗は大きくなりますが、潤滑部のグリースが排除されづらくなることで潤滑性を維持できるため、滑り摩擦の低減につながります。
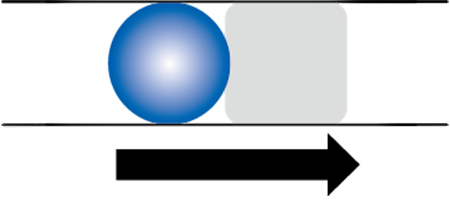
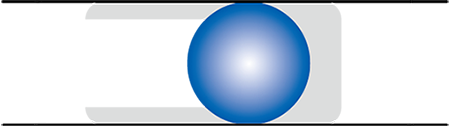
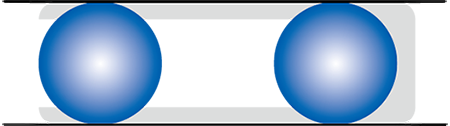
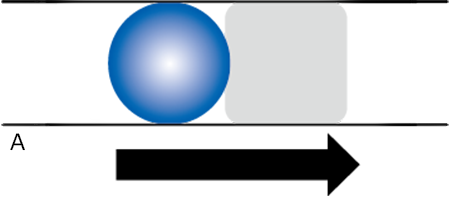

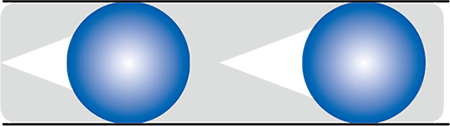
:玉
:グリース
:玉の回転方向
- A:停止状態
なお、チャーニングタイプのグリースをモーター用ベアリングに使用した場合に、「定格回転に至らない」「立ち上がり電流値が大きい」「回転ムラ」などのトルクに関連した事象が発生する場合があります。そういった際には、チャンネリングタイプのグリースを使用することで改善することもあります。
ベアリング設計の工夫
溝(レース)の曲線半径と転動体の半径の比率を、溝曲率といいます。この曲率比を上げることで、転動体と転走面(レース面)との接触面積が減り、転がり摩擦を軽減することができます。ただし、曲率比を上げることで耐荷重性が下がったり、筐体への組付け時にブリネル圧痕が生じるリスクが高まってしまうため、注意が必要です。
転動体の工夫
一般的なベアリングは、転動体と軌道との接触部に局部的な永久変形が生じることで、円滑な回転の妨げとなる場合があります。そこで、転動体の材質を鋼材よりも密度の低いセラミックに変更します。これにより回転時の遠心力がかかりづらくなることで、軌道と転動体との接触部に変化が生じにくくなり、結果として転がり摩擦の低減につながります。
組込の工夫
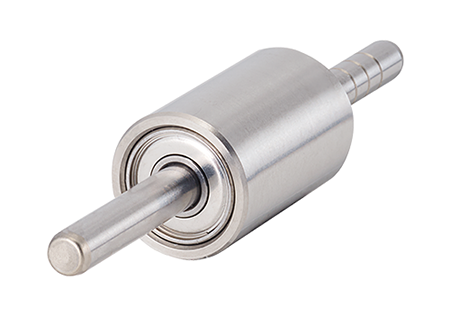
ミスアライメント(ベアリングの組付け誤差)はベアリングに高い負荷がかかることで、エネルギー損失が大きくなるだけでなく、故障を引き起こす原因にもなります。
軸とハウジングをあらかじめ組付けた状態のカートリッジベアリングを使用することで、ミスアライメントによる余計な負荷や摩擦の発生を防ぐことができます。
カートリッジベアリングを使用することで、予めベアリングの回転精度を向上させた状態で使用することができます。組込最適化対策を行うことで、ガタは0.001~0.003mm、振れは0.0050~0.0075mmまで向上させることができます。更にベアリングをハウジングなどにアッセンブリーし、軸心を出した後に組加工を施すことで、更なる振れの低減も可能です。より完成品に近い状態で加工を施すことで、振れ精度を極限まで抑え込みます。
また、重荷重によるご使用部位の耐摩耗性の向上を目的とした、表面の硬化により耐久性の向上を実現します。無電解ニッケルメッキ、硬質アルマイト、硬質クロムメッキ、窒化処理、DLCなどが対応可能です。
高効率ベアリングの活用事例紹介
エネルギー効率を高めたベアリングが、どのような用途で活用されているのか、製品の活用事例について解説します。
ファンモーター、換気扇モーター、エアコンモーター
サーバー用のファンモーターや、生活家電・換気扇のモーターなどにエネルギー効率の高いベアリングが用いられています。
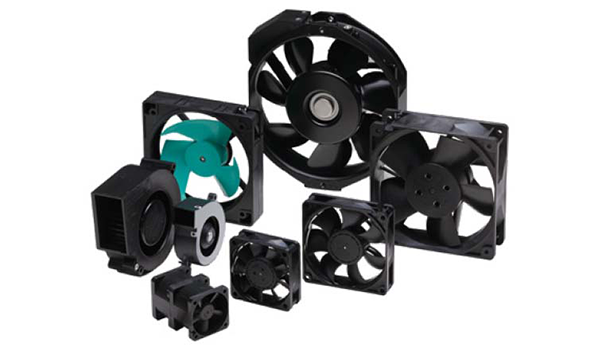
【課題】
モーターは始動時に非常に多くの電力を消費し、起動トルクは定格トルクの何倍にもなります。エネルギー損失が大きいと、電源入力から実際にモーターが回りだすまでに時間がかかり、製品の快適性にも影響します。また、エネルギー損失はモーターの発熱量にも関係しています。特にグリースの温度上昇はモーターの寿命を左右するため、エネルギー効率の向上はモーターの長寿命化を実現する上でも欠かせないものとなっています。
【対策】
ファンモーター、生活家電、換気扇など各用途に適する専用グリースを封入したベアリングを採用。それぞれの使用条件に応じた適切なグリースを選定したことで摩擦が低減し、モーターの長寿命化の実現、およびエネルギー損失の軽減につながりました。
まとめ
回転時のエネルギー損失を軽減するためには、グリースの適切な選定や高精度なベアリングの設計、転動体の材質などに工夫が必要であることを紹介しました。昨今、ベアリングはもちろん、さまざまな分野においてエネルギー損失をいかに抑えるかが求められており、特に光熱費に直結する生活家電、燃料費にも影響する自動車において省エネ性能は当たり前のものとなっています。今後も環境やエネルギーへの意識の高まりから、エネルギー効率を高めたベアリングはさらに存在感を増していくことが予想されています。
ミネベアミツミでは多様なベアリングをご用意しており、課題やニーズに合わせたベアリングのご提案が可能です。まずは、お気軽にお問い合わせください。