- Wavy Nozzle
Innovation in the method for cleaning chips from the cutting machine enables a production plan that automatically operates the factory 24 hours a day as needed.
Objective: Periodic machine cleaning work was a bottleneck that prevented the customer from creating a 24 hours a day production plan.
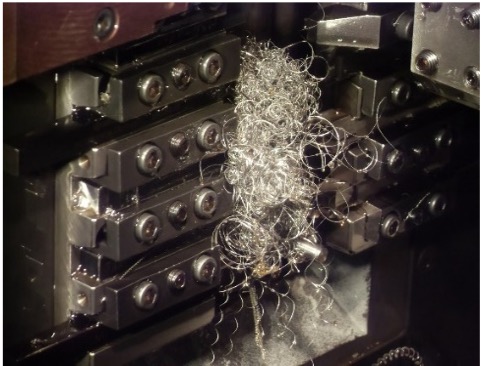
Company A processes products for industrial instruments at a factory 24 hours a day. Machine processors automatically operate at night.
Of all the processes, only the process for cutting work with the automatic gang tooling lathe could not be automated. The material was SUS stainless steel with a diameter of φ10.
If the automatic lathe continues to cut stainless steel for a long time, chips get stuck in the blades and main spindle, and lumps form due to the material's characteristics (Fig. 1). If processing continues in this state, accumulated chips damage the product appearance and lead to incorrect dimensions, and even the cutting tools get damaged. After product failures and cutting tools damage occurred over and over, the customer had no choice but to stop producing this part at night and instead only produce this part during the day, when operator can go to the machine and periodically remove the chips. The drop in productivity in the cutting process lowered the overall production operating rate. In addition, Company A lost out on opportunities and profits because they were unable to operate the factory 24 hours a day even when increased production was required.
Solution: The Wavy Nozzle blows coolant at the single point cutting tool to smoothly exhaust the chips!
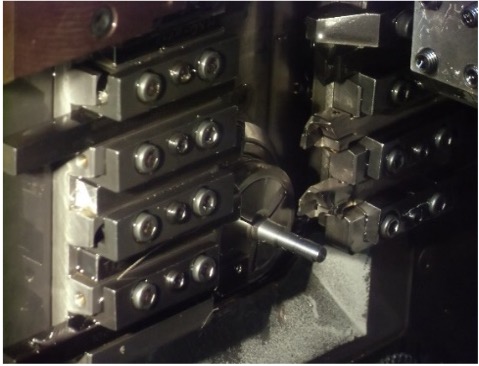
The Wavy Nozzle is a machine that swings the nozzle to spray cutting oil or air over the target. Company A adopted the Wavy Nozzle and verified its capability to exhaust chips by spraying coolant at the single point cutting tool where stainless steel is cut in a swinging manner. Our engineers also participated in the verification and determined the optimal setting values for the customer's environment in order to solve problems related to the chips. For example, they fine-tuned the amplitude and speed and controlled the spray angle. Before verifying the tuning results, we actually produced a certain amount of products for a period. We confirmed the effects immediately after introduction and verified stability for about three weeks following adoption. One month later, the customer highly appreciated how the adoption of Wavy Nozzle had guaranteed stable long-term machine operation. Nearly no chips got stuck in the product, main spindle, and cutting tools, so products were no longer damaged. This is a significant improvement. Now that chips do not lump inside the automatic lathe, cleaning is no longer required (Fig. 2).
Result: An ample production plan that enables you to flexibly respond to increases in orders and requests for short lead times
Now that periodic machine inspection and manual chip cleaning work are no longer necessary, the entire procedure, including cutting, can be automatically performed 24 hours a day. The customer no longer has to consider the costs associated with operator who remove chips and losses due to machine downtime during calculations for preparing production plans or making sudden changes. As cutting process productivity has been improved, the overall production operating rate and stability have risen, and production plans have become more reliable. Now, Company A can flexibly control its production line according to the production plan—for example, by automatically operating the factory 24 hours a day to address increases in orders or requests for lead time reduction.
Basic information
Product or service used in this case
Wavy Nozzle
Industrial field
Automotive parts, Machining of industrial equipment parts
Time taken to resolve
You can see the effects after several days. Users often determine the effects after a certain amount of production according to their internal rules; they tell us that even in these cases, they realize effects after three weeks to one month.
Fields / industries where this case study can be utilized
Cutting machining
Case Studies Related page
- With the introduction of Wavy Nozzle, they lowered defect rates and achieved their goals!【Wavy Nozzle】
- Eliminate cleaning process and use of coolant with Wavy Nozzle installation!【Wavy Nozzle】
Related page
Contact Us
Please click the inquiry type below according to your question. Each product / sales representative will respond to you.