- Wavy Nozzle
With the introduction of Wavy Nozzle, they lowered defect rates and achieved their goals!
Objective: Quality improvement initiatives are limited when chip entanglement occurs in the cutting tool.
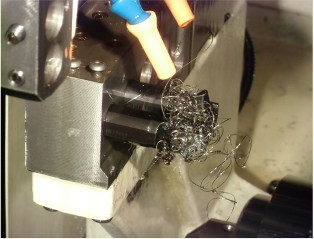
Company B can cut automotive parts. They process the material "Carbon Steel S45C" with an automatic lathe blade type with back processing.
Look at Figure 1. Due to the tangle of cutting chip in the cutting tools for rear spindle, dimensional defects occurred frequently at 2.43%.
Therefore, they were engaged in quality improvement activities with the goal of "defect rate of 1.8% or less". However, by sudden entanglement of cutting chip, they felt limited to implementing quality improvement activities only with existing measures such as cutting conditions and selection of cutting tools, and began to search for measures different from existing measures.
Solution: By putting together the piping, pressure drop is prevented.
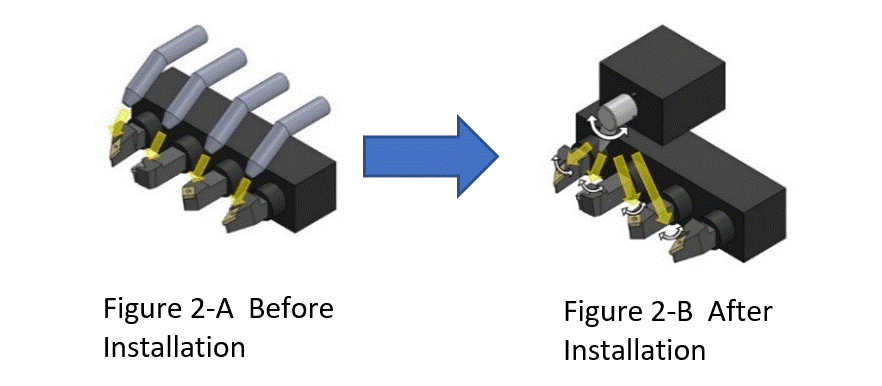
Conventional coolant nozzles have been caused by pressure drop due to the installation of fixed pipe nozzles for each tool. (Figure 2-A)
Wavy Nozzle was consolidated into one system (Figure 2-B) and set to be sprayed with each cutting tool. By consolidating and injecting piping, coolant pressure can no longer be lowered. In addition, by swinging injection, it is now available to efficiently remove chips (Figure 3).
Figure 3 Sweep out the chips
Result: Achieved a defect rate of 0.56%, compared to a target of 1.8% or less.
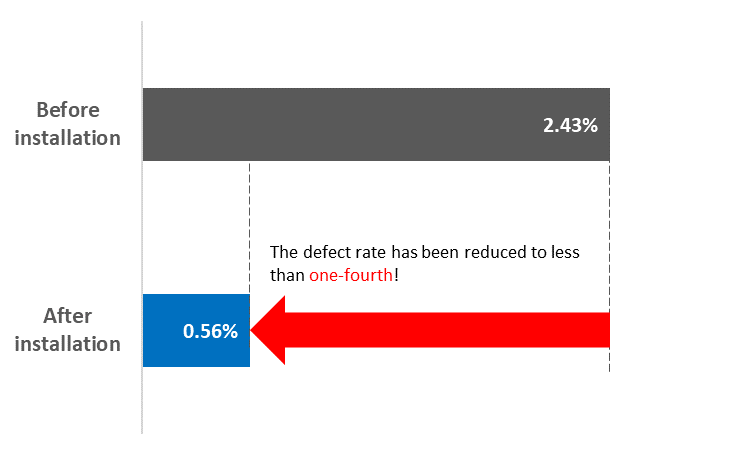
The dimensional defect rate was 2.43% due to the tangle of cutting chips in the tool for rear machining. They planned to set a quality improvement target of 1.8% or less. In addition to achieving this goal, the results improved to a defect rate of 0.56% (Figure 4).
The person in charge reported the yield improvement to the supervisor, and was satisfied with the improvement effect. In addition, he was instructed to make installations on symmetrical machines. They have been able to greatly improve yields.
Basic information
Product or service used in this case
Wavy Nozzle
Industrial field
Automotive parts, Machining of industrial equipment parts
Time taken to resolve
You can see the effects after several days. Users often determine the effects after a certain amount of production according to their internal rules; they tell us that even in these cases, they realize effects after three weeks to one month.
Fields / industries where this case study can be utilized
Cutting machining
Case Studies Related page
- Eliminate cleaning process and use of coolant with Wavy Nozzle installation!【Wavy Nozzle】
- Innovation in the method for cleaning chips from the cutting machine enables a production plan that automatically operates the factory 24 hours a day as needed.【Wavy Nozzle】
Related page
Contact Us
Please click the inquiry type below according to your question. Each product / sales representative will respond to you.