What is a strain gage?
What is a strain gage? Explanation of how it works, types, and points for selection

A strain gage is a sensor component that measures "strain (rate of change)" when an object is in tension or compression. They are widely used in the aircraft, railroad, steel, civil engineering, and construction industries, as well as for clinical medicine and rehabilitation. As strain gages are so small and rarely visible, few people may visualize how the types of applications they are actually used for.
The following is an explanation of the mechanism and usage scenarios of strain gages and how to use them for measurements, as well as key points for selecting products.
A strain gage is a sensor component that measures the strain of an object
A strain gage is a sensor component that measures the strain of an object. The amount of change refers to the extent by which an object is stretched when pulled or contracted when compressed. Strain refers the ratio of the amount of change in an object to its original length.
By measuring strain, the limits of strength of a metal component can be determined or the physical quantities such as load, pressure and torque (torsional force applied to a shaft) revealed, to name a few examples.
Strain gages are widely used in various situations such as product quality control and research and
development.
As strain gages are so small, the mass of the strain gage itself can be ignored when measuring strain. Strain gages can be used by directly attaching them to the object to be measured, such as metal or plastic, or through the use of an adhesive or similar.
1. Structure of strain gages
Strain gages are constructed by attaching a metallic foil resistive element onto an electrical insulator base (e.g., polyimide) and coating it with silicon or other material. Load is sensed by the metallic foil resistive element to measure the strain. Sizes vary from product to product, but the length of the gauge section can be as small as a few millimeters.
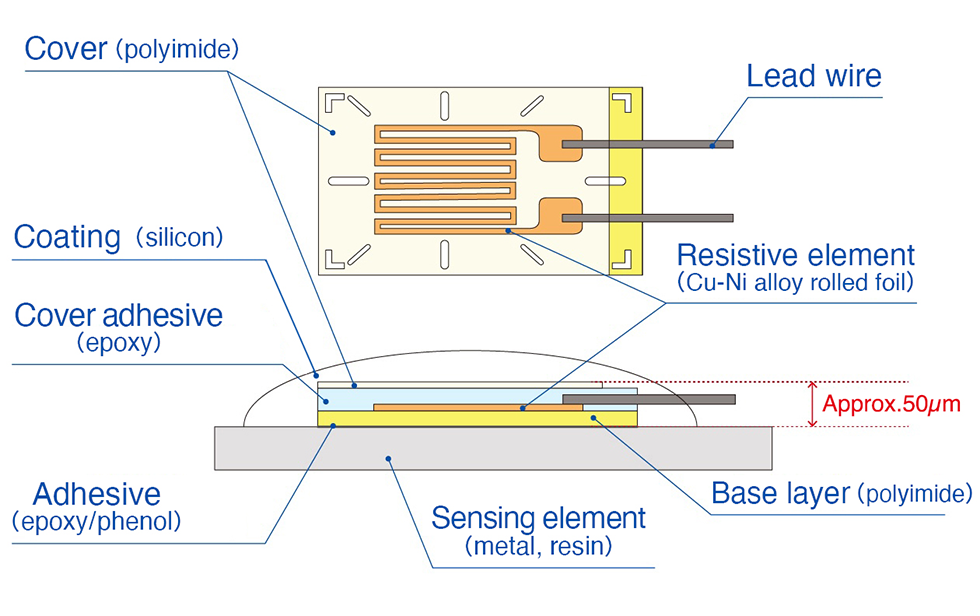
2. Strain gage mechanism
Strain gages measure strain using the mechanism whereby electrical resistance changes when a force is applied to an object, resulting in it expanding or contracting.
When a force is applied to the object being measured and it expands or contracts, the metallic foil resistive element of the strain gage attached to the measurement object also expands or contracts in proportion to that object. The amount of strain is measured by reading the change in electrical resistance that occurs as the resistive element expands and contracts.
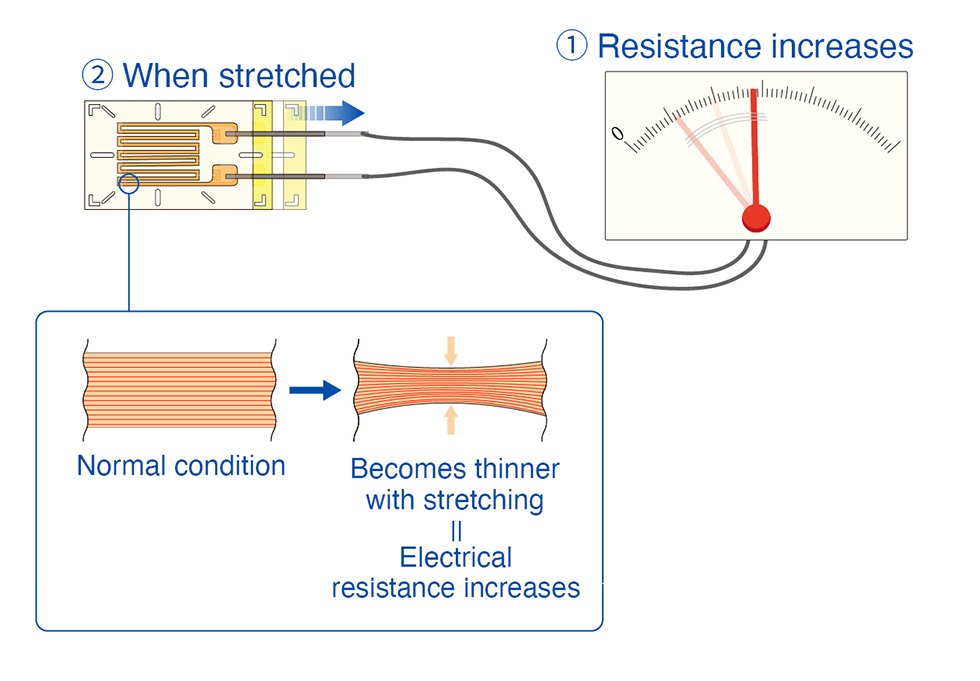
3. What are strain gages used for?
Compact and lightweight yet highly accurate and relatively inexpensive, strain gages are used for testing the strength of products and measuring load at production plants, and found in many other day-to-day products. Let's take a closer look at some specific examples of use.
Scales and weighing instruments
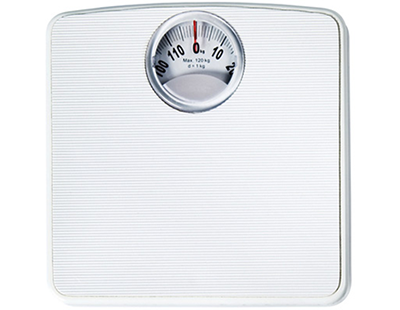
Strain gages are also used in digital scales and weighing instruments. The resistance of the strain gage when a person or object is placed on it is converted into a numerical value to indicate the weight or mass.
Computer pointing sticks
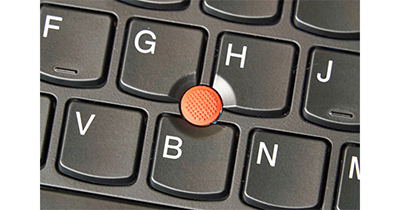
Pointing stick of computers are designed to move the cursor up, down, left, or right in the desired direction by using a strain gage to detect the amount of strain resulting from applying force with a finger.
Smartphone drop test
Strain gages are also used in strength tests related to the impact subjected by smartphones when they are dropped. A strain gage is attached to the smartphone being tested, and measures the acceleration and strain when dropped.
Torque transducer
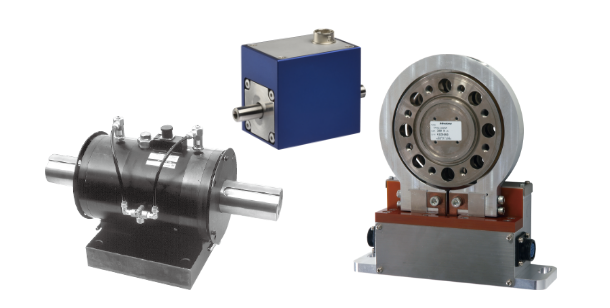
Strain gages are used in Torque transducers that measure torque (torsional force) applied to a shaft. When torsion occurs, the strain gage expands and contracts, thereby changing its resistance value—torque is measured by converting this change into an electrical signal.
See also: What is a Torque transducer? Explanation of how it works, types, and points for selection
4. How to use a strain gage
Strain gages are generally used by attaching them to the object for which strain is being measured. Note that measurement errors may occur depending on the method of adhesion.
First, the surface of the application area must be cleaned. A degreasing solvent is used to remove oil. Lift the strain gage with tweezers and attach it with adhesive or other means so that there are no bubbles remaining. After the adhesive has set, ensure appropriate moisture-proofing treatment.
5. Equipment required for strain measurement
As the resistance that can be measured with strain gages is so small, resistance is converted to voltage to calculate the strain. To convert strain into voltage and display it as a numerical value, a strain measuring instrument must be connected. The strain measuring instrument receives the signal from the strain gage, amplifies it, and displays the numerical value digitally.
DC type dynamic strain amplifier "DAS-406C"
A strain measurement instrument with high sensitivity and wide frequency response from DC to 200 kHz. In addition to strain, the DAS-406C is able to measure stress, pressure, torque, vibration, and acceleration, and is used for a wide range of applications, including simple instrumentation amplifiers.
Bridge box
The bridge box efficiently converts minute changes in resistance caused by strain on the gage into voltage using a Wheatstone bridge circuit. Connect the strain gage leads to the terminals and the plug portion to various measuring instruments.
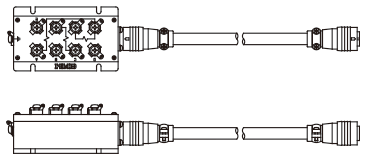
Strain gage selection
Strain gages come in a wide variety of sizes, with gage lengths ranging from about 0.2 mm to 8 mm. As different products have different resistance values, select a type that is appropriate for the required measurement target.
The materials and adhesives also differ in the temperature range in which they can be used. Different types should be used depending on whether there are temperature variations in the environment being measured, such as when the object being measured is subject to high temperatures or located in a harsh environment.
MinebeaMitsumi's polyimide foil strain gages, for instance, are able to handle temperatures from -50°C to 200°C when heat-curing adhesives are used with heat-resistant wires and terminals.
In contrast, if epoxy foil strain gages or polyimide foil strain gages are used, the temperature range is from -30°C to 70°C unless the adhesive and other materials are within the compatible temperature range.
6. If you need a strain gage, contact MinebeaMitsumi an inquire about our extensive product
Strain gages are used in research and development, such as testing the strength of products, and are one of the components of day-to-day products like scales. Their high level of measurement accuracy and ease of handling make them suitable to a wide range of applications in many fields.
MinebeaMitsumi's strain gages have excellent sensitivity, stability, and fatigue life, and their wide usable temperature range enables strain measurements in a variety of situations.
Furthermore, FEM analysis enables the design and proposal of the most suitable resistor patterns for targets being measured, such as two-element (half-bridge) or four-element (full-bridge) configurations. If you are seeking to deploy strain gages, don't hesitate to send us an inquiry.
Examples of Customization
-
- Design
of gage patterns
-
- Modified layout of
gage patterns
-
- Modified layout of
gage tabs
-
- Modified
vinyl wire lengths
-
- Single element
-
- Dual element
(half-bridge)
-
- Quad element
(full-bridge)
-
- Diaphragm type
Quad element
(full-bridge)
Pressure sensor
-
- Arrow feather shape
Dual element
(half-bridge)
Shear, torque, etc.
Strain gages are used in an extensive range of applications, not only for measuring direct strain but also as sensors in a wide variety of consumer products (such as vehicles, home appliances, and computers) and general industrial measurement requirements—a broad range of types are available in offering outstanding quality.
We design shapes to meet the customer's applications and required level of precision, and supply them via a reliable, high-quality mass production system.
For product-related inquiries, please contact us using the form below.
Contact Us
Please click the inquiry type below according to your question. Each product / sales representative will respond to you.